How will we move the big, heavy things?
The ten biggest questions in energy & climate tech, Question 9
Current hypothesis: Don’t ignore the hubs!
This is “Iowa 80”, which claims the title of the “largest truck stop in America”… which also, unsurprisingly, makes it the largest in the world.
This is Hartsfield-Jackson Atlanta International Airport, which is the busiest airport in America. I travel through Hartsfield-Jackson regularly, so I can attest that this title is well earned.
And these are the neighboring Ports of Los Angeles & Long Beach, which are America’s first and second most active marine ports, respectively.
I encourage you to keep these places in mind anytime you consider the question of how to decarbonize the big, heavy things which move through them. Because this question is as much about individual trucks, planes, ships, and trains as it is about the hubs where they come together to load & unload people, goods, and of course fuel.
The presumption of electrification
Think back to 2009. Renewable power was finally beginning to pick up steam. With the prospect of decarbonizing the grid no longer entirely theoretical, a scrappy startup called Tesla launched its first commercial product, the Roadster, along with a vision of battery electric vehicles as a new way of making use of clean electrons.
It’s easy to forget just how audacious this vision was, way back in 2009. At the time, there were three competing visions for the future of transport which seemed more or less equally plausible: batteries, biofuels, and hydrogen. It was not so obvious that Tesla was backing the right horse. In the US, a recent expansion of the Renewable Fuel Standard had already led to explosive growth in the corn ethanol and renewable diesel industries. Meanwhile, I will admit that a young, impressionable Andy Lubershane was still carrying around a dog-eared copy of Jeremy Rifkin’s 2002 treatise “The Hydrogen Economy”. (My wife never lets me forget that this is one of the first books I encouraged her to read, early on in our romance.)
Of course, we all know how this competition turned out. When it comes to light & medium duty vehicles, from passenger cars to delivery vans, there is now very little dispute that the best path to decarbonization is the battery electric drivetrain.
In hindsight, this conclusion seems foregone. How could battery electric drivetrains have lost?
Biofuels simply aren’t sufficiently scalable. By the launch of the Roadster, they were already consuming a concerning share of America’s corn & soybean crops, and their life cycle carbon benefits were questionable. It was obvious that we would not be able to rely on these “first generation” biofuel feedstocks to achieve really deep levels of decarbonization.
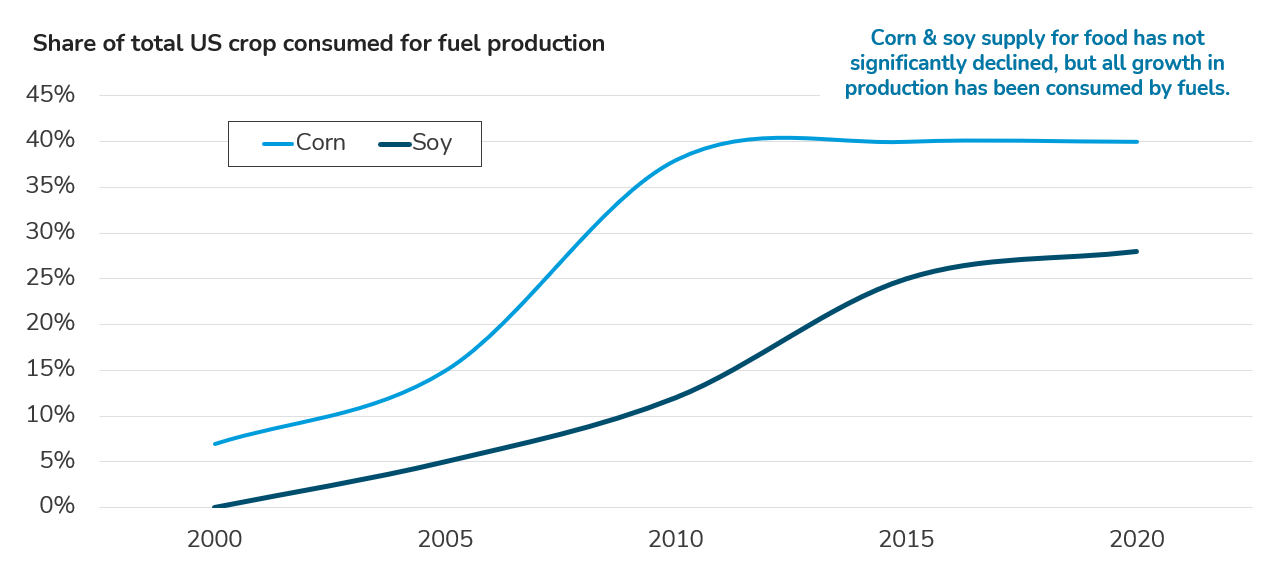
As I discussed in a recent post, “second generation” biofuels made from woody crop waste could potentially play a modest “best supporting actor” role in the energy transition. However, there simply isn’t enough sustainable biomass feedstock in the world to fuel all of the big, heavy things. Most likely, there isn’t even enough to satisfy even one major class of big heavy thing (e.g. trucks, boats, or planes).
For example, consider the case of “sustainable aviation fuel”, or SAF, which is currently one of the most active low carbon fuel markets, globally. In 2021, the Air Transport Group concluded that SAF derived from biomass could only satisfy about half of the aviation industry’s needs.
Hydrogen is a different story, as clean hydrogen produced via electrolysis of water is theoretically just as scalable as the clean power it’s derived from. But the fact that electrolytic hydrogen is essentially a derivative of clean power means that it’s inherently more expensive, joule for joule. Take the cost of clean electricity, add the cost of electrolysis equipment and the cost of energy lost to the conversion process… and you get the cost of hydrogen.1
Moreover, as I explained in a prior post, this process leaves you with hydrogen gas, which is widely acknowledged to be what practitioners call a “pain in the ass molecule”. Outside of massive, industrial-scale hydrogen applications, the cost of storing, transporting, and handling hydrogen can easily add up to multiples of the cost of production. Delivery costs are especially problematic for highly distributed hydrogen applications: for example, hydrogen fueling stations at highway rest stops.
Plus, there’s the fact that the electricity grid already exists, while hydrogen infrastructure needs to be built entirely from scratch.
There are ways of turning hydrogen into… well… less of a pain in the ass. With some additional processing steps, hydrogen can be “upgraded” into a slew of more complex molecules, such as ammonia, methanol, and even long-chain hydrocarbons which can serve as drop-in replacements for the likes of gasoline, diesel, and jet fuel. The general term which is now in vogue for these molecules is “electrofuels”, because the process for making them is typically powered by even more clean electricity. This makes electrofuels ‘second derivatives’ of electricity, which unfortunately means that their cost relative to pure, clean electrons is further compounded. (I’ll come back to electrofuels, I promise...)
This brings me to electricity’s biggest advantage over alternative clean fuels: operating cost. In most situations, electricity is not only cheaper to produce & deliver than its competitors; battery electric drivetrains are also more efficient than either internal combustion engines or hydrogen fuel cells, and they require very little maintenance. The net result is that battery electric vehicles tend to be the cheapest vehicles to operate - even compared to fossil fuel vehicles.
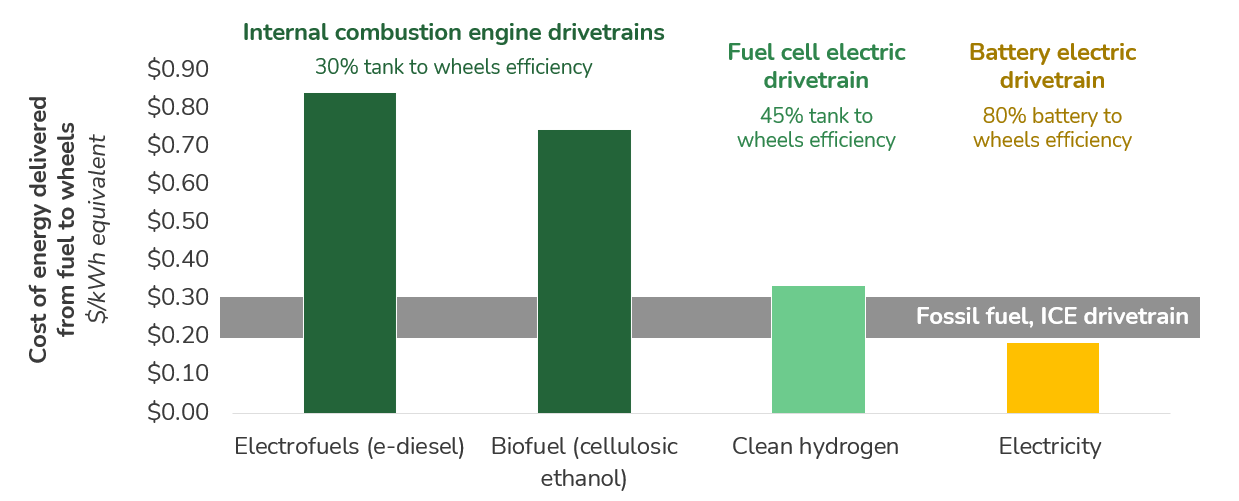
But of course, operating cost is just half of the equation (very roughly) when it comes to the total cost of ownership for a vehicle. The other half is up-front cost. This was initially a big, big problem for battery electric vehicles.
Back in 2009, the first Roadsters to hit the market were priced at over a hundred thousand dollars. More than half of the Roadster’s price tag was required just to cover the cost of its lithium-ion battery. There was no way that a few hundred dollars in annual fuel savings would make up for such an expensive battery. Hence, the idea of a mass market electric vehicle was entirely dependent on an order-of-magnitude reduction in battery prices…
I assume most Steel For Fuel readers know the rest of the story. Notably, it’s not a story about a technology breakthrough. Instead, it’s mostly a story about learning curves. Lithium-ion manufacturers, mostly in China, followed a two-part playbook from the solar photovoltaic industry (also, mostly in China):
Increase manufacturing scale by about 1,000X.
With every new factory, iterate just enough on the product in order to maintain steady performance improvements.
It’s worth taking a moment to appreciate how extraordinarily well this playbook worked. Modern lithium-ion battery supply chains are marvels of scale & sophistication. Battery cell manufacturing is probably second only to microchip fabrication when it comes to the level of precision required to achieve both high quality and throughput. It takes an enormous amount of practice… which is, by the way, mostly what economists are referring to when they talk about “learning curves”. Remember: the thing about learning curves is that it’s people who are doing most of the learning. There’s a reason that essentially all new battery manufacturing projects in the US are being developed as joint ventures with experienced Asian manufacturers.
Because of the magic of learning curves, EV batteries now boast sufficient density to quell consumer range anxiety; sufficient longevity to underpin a 10+ year warranty; and most importantly, sufficiently low prices to approach sticker price parity with internal combustion engine vehicles. And manufactuers are not resting on their laurels. Silicon anodes are happening! Solid-state technology might pan out. Startups are innovating around lithium-metal anodes; novel cathodes; and all sorts of manufacturing & architectural improvements. Amazingly, batteries seem to keep getting cheaper, denser, safer, faster-charging, and more tolerant of extreme heat & cold. (Although, notably, it’s vanishingly rare for a next-generation cell to improve on all of these parameters at once…)
Meanwhile, incumbent lithium-ion juggernauts are continuing to make progress on “established” electrode materials. See: Lithium-Iron-Phosphate, or LFP, a proven chemistry which threatens to crush many nascent competitors in the dust (especially in stationary grid storage, which is much less sensitive to energy density). And sodium-ion, a closely related battery chemistry has an even more competitive cost entitlement than lithium-ion.
I do worry that some of this hard-won progress is fragile, because the country which has made the most progress down the learning curve so far has been China. The biggest risk to the future of electric vehicles is no longer the pace of technological progress; it’s the risk of a schism between the Chinese battery supply chain and Western markets. (Hence, the third big question I addressed in this series was: Will the EV supply chain hold?)
Stepping back, this much is clear: The falling cost of batteries has given electrification a decisive edge in the race to decarbonize light & medium duty vehicles. So: Why not all of the big, heavy vehicles, too?
Why not electrification?
There are two major constraints holding back electrification in heavier duty vehicles.
Battery (energy) density.
Charging capacity.
Let’s start with battery density.
Yes, batteries are amazing, and they seem to be getting more amazing practically every month.
But unfortunately, they’re not on track to become amazing enough to power the biggest, heaviest things. The most obvious problem with batteries for the heaviest duty vehicles is that most of these vehicles are already weight & space constrained. Batteries are currently two orders of magnitude heavier than liquid hydrocarbons, and completely out of league with hydrogen, which is the lightest possible energy carrier. They also require nearly twenty times as much space to carry the same amount of energy as a diesel tank, and twice as much space as compressed hydrogen.
Batteries can get away with such poor energy density in light & medium duty vehicles because, in most cases, those vehicles have liters and grams to spare. They’re able to add a big, heavy battery and still operate safely on normal roads, with enough room left over for passengers and a few suitcases.
This is not the case for bigger, heavier vehicles which need to travel farther in between stops for fueling. Even optimistic targets for next-generation battery density are simply not enough to make batteries a viable option for vehicles with ultra tight weight, volume, and range tolerances.
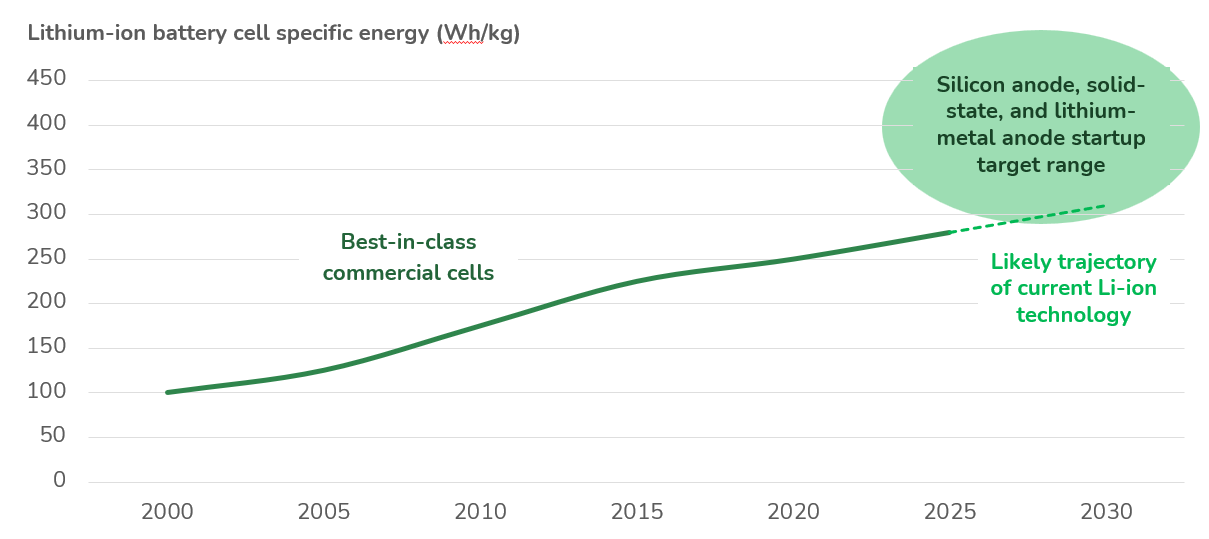
E.g. Trucks
Tight weight, volume, and range constraints, you say? Let’s talk trucks. Specifically, Class 7-8 trucks. Big, heavy semi-trucks.
It’s possible that these trucks could all go fully electric, eventually. They are indeed sensitive to weight, volume, and range; however, it will probably take just one more leap forward in battery technology to make the vast majority of trucks into viable targets for electrification. In fact, the vast majority of freight shipments today are less than 250 miles, which is already in scope for a few first generation electric semi-trucks.
However, the small number of trips that are longer than 250 miles actually account for the majority of total ‘ton-miles’ traveled, because of the fact that these trips are so much longer!
Moreover, adding enough battery capacity to ensure that a truck has sufficient range for all of the trips it might need to make is an expensive proposition. Even if the majority of trips are less than 250 miles, a handful might require traveling significantly more distance between stops, and a few might be in very cold conditions (which dramatically reduces range), etc, etc. Adding enough battery capacity to prepare for these scenarios is probably going to be necessary to give operators the confidence to electrify more than a small share of their fleet. Unfortunately, that means adding to the cost of the vehicle, plus adding weight and taking up precious space which could otherwise be allotted to cargo.
Perhaps even more problematically, bigger batteries will need much higher capacity chargers.
Let’s talk about charging capacity.
Consider a fleet of fully electric trucks. Some (lucky) trucks are able to return to a depot every evening and charge relatively slowly overnight; but many will need to recharge out on the road… at least every so often. In order to travel just half the distance that a typical long-haul truck travels in between breaks, a fully electric truck would need about a megawatt-hour of battery capacity, which is the equivalent of about 10-15 light duty EV batteries. Such a large battery would necessitate a two megawatt charger, in order to facilitate thirty-minute turnarounds, say, at a depot or a highway rest stop. Today’s “ultra” fast chargers are typically rated for less than a fifth of that capacity (a mere 350-375 kilowatts).
Building a 2 MW charger is expensive, and the expense is not just in the charging station itself (although, to be clear, we’re talking about a cord as thick as your arm). The expense is also in the grid infrastructure required to serve additional peak electricity demand at sites with multiple chargers. From the standpoint of the power grid, large truck depots and rest stops could easily swell to the scale of large towns or small cities. For example, here’s an analysis of around 70 prospective charging sites in New York & Massachusetts by the electric utility National Grid, whose landmark 2021 “Electric Highways” study illustrated the scale of the challenge.

Hence, from the trucks themselves, to the chargers, to the grid, the cost of electrification is likely to balloon as we seek to electrify more and more miles, for more & more vehicles.
This level of electrification also raises a classic ‘chicken & egg’ problem. Truck operators will be hestitant to electrify a substantial share of their fleet until they’re confident that they can charge vehicles quickly, outside of a depot, when the need arises. This is especially true for small, independent operators with just 1-5 trucks, whose fleets account for a surprisingly large share of the total market. Meanwhile, electric utilities tend to have a tough time getting regulatory approval for major investments in grid infrastructure until they can point to a very clear demand signal.
This is why, as bullish as I am in the long, long, long term future for electrification, I think we need to be realistic about what’s practically achievable within the next couple of decades.
And fortunately, the long, long, long road to full electrification does not preclude investments in partial electrification along the way. I find myself drawn to ideas like Range Energy’s electrified tractors, which are designed to partially pull themselves. This strategy enables operators to substitute electricity for a share of their diesel fuel on essentially any route, without requiring a commitment to fully electric tractors or multi-megawatt charging. I’m similarly enamored by Revoy’s vision for a highway-spanning fleet of ‘secondary’ electric tractors which are designed to sit in between a regular tractor & trailer. They’re small, driverless units intended to supplement the motive power of a primary tractor. Most notably, they’re capable of swapping themselves in and out when they arrive at charging stations. This concept could hypothetically electrify even more miles without requiring any ultra-fast charging, and enable operators to ‘refuel’ as quickly as they’re accustomed to with diesel.
I suspect that these types of semi-electrification solutions could ultimately be a better long-term option than fully electric tractors, in many settings. If we could electrify the lion’s share of heavy duty miles without triggering the need for massive grid upgrades, the remainder could be much more realistically & affordably addressed with our limited supply of biofuels, or with hydrogen. Also, these sorts of tools could serve as range extenders for fully electric trucks - even over the long, long, long term. I’m a big fan!
E.g., Aviation
Tight weight, volume, and range constraints, you say?
Sure, we might electrify some very small planes making very small “hops”. For example, Cape Air flies a bunch of routes from big cities to nearby vacation destinations, and has signed a landmark LOI for 75 electric “commuter” aircraft from Eviation. This is really neat! However, I don’t believe it should be viewed as a first step towards electrifying larger planes or longer flights.
According to a fantastic report by the International Council on Clean Transportation, electrification is only viable, at present, for a tiny sliver of air traffic served by very small planes. Even if the gravimetric density of batteries were to double, electrification would still be impossible for the vast, vast, vast majority of flight-miles.
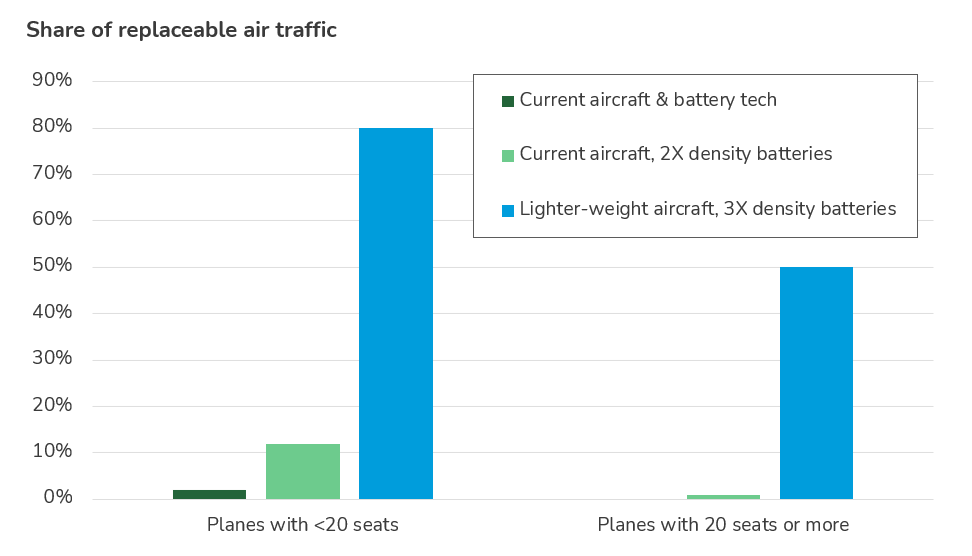
Let’s say, for sake of discussion, that we found ourselves with a novel battery chemistry which could store 600 watt-hours per kilogram, at the pack level. This is undoubtedly moonshot territory, but it’s theoretically possible. (Although, I should point out, that’s about twice as dense as the targets I’ve observed among battery chemistry startups.) Let’s also assume we could reduce the weight of the remainder of the plane, sans battery, by about 15%. This is probably also achievable, although we shouldn’t downplay the challenge. After all, weight has been a critical factor in aircraft design since the beginning of human flight!
Neither of these advances would break the laws of physics or chemistry, and taken together, they could theoretically open up a much greater share of air travel to electrification. Except…
Except… you thought truck stop charging requirements were rough?!? Ha!
Consider even the mildest scenario for aviation electrification: hybrid planes. By my calculation, an average mid-sized, 100-ton plane would require a battery containing about five megawatt-hours of energy in order to “fly electric” for even 100 miles out of a typical 500 mile flight. Filling that battery in half an hour would require charging at a rate of 10 megawatts, which means that a single hybrid plane charging at a single gate would double the peak power demand of a small airport! Hybridizing all of the planes at a mid-sized airport in this way would require additional electricity supply on the order of a nuclear power plant.
The challenge of building all of the electrical infrastructure required to serve this kind of demand, amidst the 24/7 operations of an actual airport, is practically inconceivable. Frankly, it’s going to be plenty difficult just to electrify all of the supposedly “easy to electrify” vehicles & ground equipment we rely on at airports.
In a recent study, the mobility solutions company Enterprise collaborated with the utility company Xcel Energy in order to assess power demand needs from airport electrification, setting aside the planes. They found that electrifying ground-based equipment and rental vehicles alone would roughly quintuple peak electricity demand at two representative airports: Minneapolis & Denver. Here’s Denver…
The study finds that utilities probably need to start building new infrastructure immediately, just to keep up with electrification happening on the ground.
In short: keeping up with electrification at airports will probably be a heroic effort, and that’s setting aside any electrification of actual flight.
E.g., Maritime
Electrifying big boats is probably a bit more of a realistic prospect than electrifying big planes. But, that’s not saying much.
Similar energy density challenges hold. Here’s the space that fuel oil takes up in a standard twenty-foot-equivalent container vessel...
And very roughly, here’s the space that a battery would take up in order to move that same ship, over the same distance…
I won’t belabor this point. Yes, it’s theoretically possible that advancements in battery technology could close this gap by an order of 2-3X. Big changes in the paradigm for cargo ship design & operations could also make electrification more feasible.
However, from the standpoint of charging infrastructure, electrifying marine ports is probably an even more daunting prospect than electrifying airports.
Marine ports sit at the nexus of both heavy duty shipping and ground transport. In addition to fueling massive container ships, ports also serve as fueling hubs for swarms of “drayage” trucks, which spend all day ferrying cargo to and fro among crowded loading docks. Take the Port of Long Beach, which I highlighted at the beginning of this post, and is an early leader in the electrification of cargo handling equipment. In 2021, the port authority published a study of what it would take to decarbonize the roughly 1,600 drayage trucks that call the port home.
Figuring out how to upgrade the electrical infrastructure serving the port in order to deliver this kind of power is a monumental task. For context, back in 2011, the very same Port embarked on a ten-year effort to electrify nearly all of the cargo handling equipment and to provide “shore power” to ships at just one out of seven of its major cargo terminals. They electrified 18 ship-to-shore cranes, 5 intermodal cranes, and 70 yard gantry cranes. I believe that this was the largest global port electrification project of its kind, to date.
The entire project took ten years. Four of those years were required for the electric utility, Southern California Edison, to build a new 66 kV subtransmission line and four new substations, plus string miles of additional conductor.
… and that’s before they considered electrifying a single tugboat.
It’s the infrastructure, stupid (feat. hydrogen)
Of course, it’s technically possible to build all of the electrical infrastructure we’d need to charge all sorts of big, heavy things. But frankly, the idea of expanding the grid at the pace required is beginning to strain credulity. I’ve personally spent much of the past year hollering to anyone who’ll listen about an impeding “Electricity Gauntlet” which is already making it difficult for utilities to keep up with power demand growth. The world is waking up to the magnitude of this challenge.
So, let’s return to those alternatives to the battery electric drivetrain.
What about hydrogen???
For most fueling sites, the prospect of building out an entirely new hydrogen delivery system tends to be even more daunting than upgrading the electricity grid!
But ports & airports are not “most fueling sites”. The extraordinary scale of energy demand at these sites probably levels the playing field for hydrogen; in fact, it might even give hydrogen an edge. It’s almost always cheaper to move massive amounts of energy in the form of a gas, via pipeline, than in the form of electrical current, via transmission line. There are many reasons to believe that hydrogen infrastructure will benefit from economies of scale. Meanwhile, we’re already seeing electrical infrastructure struggle with demands for additional expansion.
Picture a massive field of wind turbines, paired directly with large-scale electrolysis equipment, pumping hydrogen into a pipeline which runs a few hundred miles into one of these hubs. Now, picture the same setup at two hubs with lots of back & forth traffic between them, and you can start to see the inklings of a practical hydrogen fueling strategy…
Perhaps this is why hydrogen seems to have taken an early lead when it comes to decarbonizing yet another class of big, heavy thing… a vehicle intended to travel back & forth, over long distances, between two depots. Of course I’m talking about TRAINS. Three leading European train manufacturers - Alstom, Siemens, and Stadler - have already launched hydrogen-fueled models, and are beginning to deploy them.
Hydrogen also has a big advantage over batteries when it comes to range and fueling rate. It’s the most gravimetrically dense transport fuel, and it flows into a vehicle nearly as quickly as diesel. However, volumetric density is still a major challenge. Hydrogen can store about twice as much energy in the same volume as a lithium-ion battery pack, but that’s still nowhere near as much as hydrocarbons. Hence, most hydrogen-fueled vehicles need to be fully redesigned, essentially starting from a clean sheet of paper. And no matter how cleverly we’re able to design new vehicles around the need for hydrogen tanks, those tanks inevitably take up a bunch more space.
So, while I think hydrogen is a better fit for the biggest, heaviest vehicles than batteries, it’s still not an ideal choice. There are only a few bold companies pioneering hydrogen aviation (e.g. ZeroAvia, Universal Hydrogen), and practically nobody is trying to make hydrogen work for cargo ships.
The best jet fuel… is jet fuel
At last, that brings us back to “electrofuels”, which refers to fuels that are produced by ‘upgrading’ clean hydrogen into denser, liquid molecules using processes predominantly powered with clean electricity. Effectively, these processes are trading additional cost, in the form of processing equipment and energy, in exchange for much better energy density.
The two electrofuels most commonly considered for heavy duty shipping are ammonia & methanol.2 Both have their proponents & detractors. At Energy Impact Partners, many of us have naturally sorted ourselves into what we call “Team Ammonia” and “Team Methanol”, with lots of sparring back & forth. I’m ashamed to say that I’ve switched teams twice now, as I see compelling arguments on both sides. Net-zero ammonia is inherently cheaper to produce, because net-zero methanol requires captured carbon. But, ammonia is waaaay more toxic, which has ramifications for the cost of fuel delivery & storage, both in ports & on ships.
When it comes to aviation, however, nearly everyone in the industry concurs that only one variety of electrofuel will really do the trick: the mix of long-chain hydrocarbons we already call “jet fuel”.
It’s possible to synthesize clean hydrogen and carbon dioxide into a net-zero version of this blend, using essentially all established processes, outlined below. There are also more efficient pathways in the works, such as the process being developed by EIP portfolio company Metafuels to convert methanol into jet fuel with high selectivity.
So-called “E-Jet” will undoubtedly be more expensive to produce than its fossil fuel namesake, probably by an order of three or four, on par with the most expensive biofuels. However, the wonderful thing about jet fuel… is that it’s jet fuel. It doesn’t require any change in aircraft design, operations, or fuel delivery infrastructure.
That could easily be enough to make E-Jet a commercial winner.
However, E-Jet and other synthetic hydrocarbons do face one more existential question. It’s a question I’ve been wrestling with since I first learned about the concept a few years ago.
In order to achieve a truly net-zero emissions profile, the carbon that electrofuels contain needs to be sourced from the atmosphere, via one of many processes we’ve come to refer to as “Direct Air Capture”, or DAC. But… if we’re able to deploy DAC for a reasonable cost, say $200 per ton of CO2 or less: Why don’t we just sequester the carbon we capture underground, and continue burning fossil fuel? That would avoid the need to produce clean hydrogen and a bunch of expensive, intermediate process steps, and you’d end up with the same net carbon balance. Hmm…
I’m going to punt on the answer to this question until the next (and final) post in this series: Will CCS make a lot of these other questions moot?
Decarbonize the hubs, decarbonize the vehicles
There are still way too many uncertainties to predict with much confidence how we’ll decarbonize any individual class of big, heavy vehicle. But as we consider all of the various pathways, I’m convinced it will behoove us all to pay close attention to the hubs where those vehicles come together to fuel. Building the energy infrastructure to serve those hubs will probably be an even bigger challenge than designing an entirely new new truck, ship, or plane. We’ll progably end up with a whole lot of electrification, but limitations on battery technology and the pace of electrical infrastructure deployment mean that we need to prepare for hybrid approaches.
So, the next time you find yourself pulling over at a highway rest stop, or pacing around an airport terminal looking for a place to plug in your phone… Take good notes!
Please check out the rest of the Ten Biggest Questions in Energy & Climate Tech.
And also, please subscribe!
Zero-carbon hydrogen can also be produced by cleaving carbon atoms from methane molecules in various ways, and then burying the carbon before it has a chance to enter the atmosphere. These are all essentially forms of “pre-combustion” carbon capture & sequestration. It’s possible that these methods could produce hydrogen more affordably than electrolysis, and their deployment is theoretically limited only by our ability to keep securely sequestering carbon underground. (I’ll address this caveat in my next post in this series.)
Yet, no matter how hydrogen is made, it’s not a very practical medium for delivering energy to highly distributed locations – for example, the tens of thousands of gas stations at which we currently refuel passenger vehicles today. All of those gas stations are already connected to the electricity grid. But of course there is no such hydrogen grid, and as I pointed out in a prior post, building one at the scale of our existing energy delivery networks is almost surely a pipe dream (pun intended). I can foresee us building out very large-scale hydrogen infrastructure to move massive quantities of the stuff from one point to another; but hydrogen is too much of a “pain in the ass” molecule to be ferried all over the place.
Ammonia & methanol are not always included in the “electrofuels” category, but I think they ought to be as long as they’re produced via primarily electrically driven processes.
Thanks for the article and the summary on the Catalyst podcast. Thought you might be interested to see what’s happening in Tianjin, China - https://www.xdgro.com/article/detail.html?id=839&language=en